WHY CONSIDER IMPROVEMENTS
Although I seem to have gained a reputation for being somewhat of a Healey modifier I still believe strongly that a standard Healey in good mechanical condition is a fine car to drive and preserve, and I only offer what follows in response to several enquiries that I have had on the subject. I do not consider myself to be an expert, but I have some experience and what follows is based upon that; furthermore I’m sure that most of what I’m going to say will be obvious to those who have considered the subject in any depth but, for those who haven’t, this should be a good starting point .
Because the big Healey is the epitome of a “sports car” it is not unreasonable to think that perhaps it should handle in a sporting like manner. It is pretty disappointing to take your car out to a friendly gymkhana or similar event and find that no matter how well you drive 1200c.c. rice rockets are completing the course in half the time it takes you and your Healey. What I’m describing below should result in some respectable improvements and is, for the most part, easily reversible; I’m not advocating modifying the car so dramatically that it looses its classic appeal.
SOME BACKGROUND
Up until 1965 all big Healey’s used the same suspension which dates from 1952. Many of the components were probably designed for a cars built immediately after WWII. The rear suspension of the big Healey is an interesting study in design compromises. In the interests of styling and to minimize manufacturing costs Donald Healey opted to use a rather outdated “under slung” ladder frame for the 100. I’m pretty sure that the Healey was the last mass produced car to use this design. One of the most demanding compromises which has to be addressed with this type of design is the spread of the main frame rails. Positioning the frame rails far apart improves the rigidity of the frame but places some major limitations on the suspension. With the Healey I believe the spread of the frame rails was determined by the front suspension and that the rear was built around the result.
UNDERSLUNG FRAME
The problem with the under slung design is that the available suspension travel is limited by a factor of the distance from the underside of the rear axle to the ground. In the case of a Healey the total travel available is less than 12 cm. Common practice in suspension design is to maintain the car’s normal ride height at or slightly above about mid travel. This means that the axle has only about 6 cm of available movement either up or down, and that is not very much. If you watch the suspension of a car driving next to you some time, you will see that an average car uses 10-15 cm of travel along a relatively smooth piece of highway.
The Healey design did produce a “firm” ride but, for cross ply tyres, which were all that was available in those days, the suspension was reasonably adequate.
HEALEY SUSPENSION IN THE 21ST CENTURY
Radial ply tyres became commonly available in the early 1960s and their improved grip means that they can generate forces in suspension systems that are substantially higher than could be generated with the bias or cross ply tyres. As a result, with good tyres and some not very aggressive driving, the body roll of a Healey can be quite significant. Body roll in itself is not necessarily a bad thing, but it can have some negative effects when it causes excessive changes in camber of the wheels. i.e. their inclination relative to the ground.
However in the case of a Healey with its under slung frame, there is another major problem in that the body roll can be so significant that the rear frame on the inside of the turn rises sufficiently to contact the axle, which in turn lifts the inside tyre off the ground.
WHEEL LIFT
This has two immediate effects. Firstly the inside wheel spins because it cannot transfer the engine power to the ground and secondly the back of the car tends to step sideways. This sideways stepping is because tyres, particularly radial ply tyres in motion, behave a little oddly. Explained in simple terms, two tyres carrying 500 pounds each will have considerably greater resistance to side thrusts that one tyre carrying 250 pounds and the other carrying 750 pounds or in other words lift off one rear wheel and because the load on the rear tyres is suddenly transferred completely to the outside tyre things go very pear shaped indeed.
THE FIX
To rectify this situation we have several options.
1. We could fit stiffer springs. The problem is this would result in an even harsher ride, possibly okay for a smooth race track but definitely not ideal for street use.
2. We could increase the available space for rear axle travel. This is the solution that B.M.C. adopted in 1965, but it required some fairly extensive frame modifications which are out of the question for most people.
3. We could add roll stiffness to decrease the amount of body roll in turns and this is the course we will pursue here.
INCREASING ROLL STIFFNESS
Roll stiffness can be easily increased by installing anti roll bars. The front of a Healey already has an anti roll bar and you can stiffen this a little by eliminating the softness of the bushes or considerably more by fitting a thicker bar. Increasing the front roll stiffness results in the outside front wheel supporting more weight in the turn and the car staying more level however, as a result of the uneven tyre loading thing mentioned above, this change alone will produce massive understeer. Understeer, for those not familiar with the term, means you turn the steering wheel but the car to a greater or lesser degree carries on straight ahead.
To achieve the desired result roll stiffness has to be increased both front and rear, and then balanced between ends to keep the tyre weights where you want them through the turn. When this is done correctly the weight transfer in the turn will be evenly distributed between the front and rear wheels and this will produce the maximum grip.
SOME THINGS TO CONSIDER
1) Increasing roll stiffness will have a detrimental effect on the way the car negotiates one side bumps but a further modification; fitting tube shocks will improve this dramatically.
2) Installing most of the available rear anti roll bar kits involves welding to the frame.
(I have developed a design for a rear anti roll bar which requires only the drilling of 4 holes for installation but as yet I have not had an opportunity to test the design).
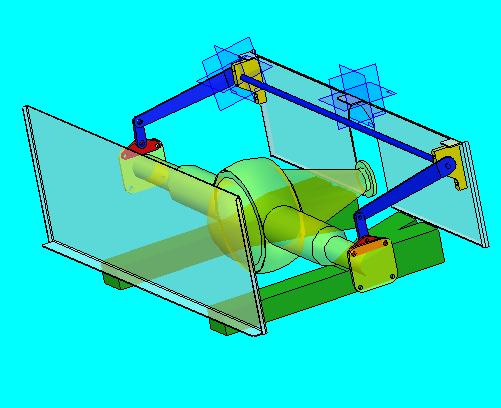
REAR ANTI ROLL BAR SYSTEM UNDER DEVELOPMENT
3) When it comes time to make adjustments remember; the stiffness of an anti roll bar increases as the fourth power of its diameter so a very slightly thicker bar will be substantially stiffer.
I hope that all helps.
Hi Alan, thanks for the input and recommendations. I had considered putting the anti roll bar (ARB) behind the axle but there are some issues which encouraged me to move to the front. As usual there are a bunch of compromises involved.
1). The Panhard rod is in the area behind the axle which limits the available room and would require that the ARB be elevated sufficiently from the frame to position it high enough to prevent interference with the Panhard Rod. This would require some sort of bracket to elevate it from the frame if it was to be frame mounted. I did mount the ARB on AHX12 behind the axle on a pair of staggered mounts as in this picture.
2). Because the original arrangement on a Healey produces a car which is fairly well balanced the rear ARB needs only to produce sufficient anti roll moment to counteract any increase in the moment provided by the improvements in the front ARB (more or less). My experience with AHX12 and my “S” has been that anything more than an 11 mm bar with fairly long lever arms is too much for this application. The axle center line is 25 cm from the forward (heel panel) but only 16 cm from the trunk front wall. I selected to use the forward panel to permit longer lever arms.
3). Attaching the ARB bearings using standard BMC type mounts or any others for that matter to the frame would be very difficult to achieve without welding because of its hollow box construction. I had considered making a 2 part collar which would clamp around the frame, perhaps with a thin rubber liner but this started to get complicated and could be a real problem if it was to come loose.
4) I have an alternate plan for the forward type ARB bearings based upon the rear shock mounting bolts which is what I did with my 100S back when i circuit raced it and, if testing proves that the heel panel attachment points weren’t up to the task, that is my fall back plan.
5) My experience with rose jointed links has not been too good. Maybe I’m using the wrong type but I have found that they develop play after only a few thousand km of use. Any recommendations would be gladly received.
Michael –
Your rear anti roll bar design looks interesting but I think you have to be very careful of the torsional stresses on the rear bulkhead… this bulkhead is not that strongly attached to the frame and anti-roll bars work best when they are attached firmly to the frame. You may end up ripping off the rear bulkhead after only a few races.
I think you would be much better off running the anti-roll bar on the backside of the axle (rather than the front as you have shown), attached with standard healey anti-roll bar brackets to the top of the frame and custom rose joint links hooking up to the axle. This would work well also because the anti roll bar, when in action, would be acting in a compressive force against the frame so the chance of ripping out the mounting bolts of the brackets on the frame would be essentially nil.
The lever arm could possibly be too short so you should have the roll bar’s lever arm come up and over the top of the axle and then connect it roughly in the same spot or even slightly forward on to your illustration.
Does this make sense?
Alan
I believe I can see the model and thanks for the explanation.
Best–Michael
Hi Michael,
Thank you for your very kind comments. I’m enjoying putting this blog together and it is very gratifying to hear that it is of interest.
Let me try to answer your question which, by the way, is a very good one.
This concept is indeed one which is difficult to grasp. It all has to do with dynamic corner weights.
One way to think of it is this:
Consider a car which is stationary on a very grippy road with a cable attached to the center of gravity (on a Healey that just happens to be exactly half way between the front and rear wheels and about 19 inches above the road.) Pull on the cable directly at right angles to the car’s axis and parallel to the road. (This force represents centrifugal force)
The car would try to lean over, body roll, however our car has no front springs (solid suspension) and incompressible tyres. In this case the car could not lean unless the frame twisted between where the cable is pulling and the front suspension. If you pulled hard enough eventually the inside front wheel would come off the ground but the rears would both stay on the ground. (Just like a car lifting a wheel in a corner)
This is essentially what happens if you have a very stiff front anti roll bar. The rear wheels, because the car doesn’t lean over, see less change in relative load but at the front there is a substantial redistribution of load from the inside wheel to the outside.
When the roll resistance, which is a combination of the spring rate and roll bar influence is exactly the same front and rear the car will lean over and the transfer of load from the inside wheels to the outside will occur at exactly the same rate front and rear.. This would constitute a neutral handling car.
Please let me know if this does not help and I will be happy to give it another shot.
Michael Salter
Michael–
I can’t tell you how much I enjoy your blog. It is extremely well put together and reflects much intelligence–yours I must assume!
I’ve made many of the changes that you recommend on my 100–the heavier 7/8″ bar in front, the anti-sway bar in back and tubular shocks all around, all contributing to a better if somewhat stiffer ride. In fact I am to the point of conceding that in order to take further advantage of these upgrades I must put on larger section tires (I’ve been using Michelin zX 175’s in part because I like their tall, narrow appearance plus the increased ground clearance) such as many use. But I digress….
In your article on ride and suspension you make the following statement:
“Increasing the front roll stiffness results in the outside front wheel supporting more weight in the turn and the car staying more level however, as a result of the uneven tyre loading thing mentioned above, this change alone will produce massive understeer.”
Since a heavier front anti-roll bar will also have the effect of lessening body roll and keeping the inside front tire better in touch with the road in a turn, why would that not tend to minimize understeer by preventing inside wheel lift and so increasing the front wheels’ ability to steer through the turn, as opposed to inducing massive understeer as you state? I know that what you say is common knowledge and I have read it in other treatises on handling, so obviously I am missing something. Can you enlighten me?
Best (and keep up the great work)–Michael Oritt
I will probably make the prototype roll bars some time in the spring when I get a “round 2 it” 🙂
Glad you liked the post Howard. Hope it points you in the right direction.
Regarding the discrepancy between your manufactured date and the title date I would suggest this.
The car probably arrived in the U.S. in Jan or Feb of 1960. My bet is that it sat in the distributor’s yard for a couple of months then was sent off to a dealer.
It then sat on the dealers lot for a few more months before it sold in say… Sep 1960. That is essentially the new model year for North America so the dealer registered it as a 1961.
Michael,
Very interesting. So when are you going to make it? Keep up the innovations for the improvement of an already great car.
Lin Rose
60 BT7 #4044
59 Bugeye
Great site:
Very,very helpful ideas especially the roll (sway) bars.I plan on beefing up the suspension and adding roll (sway) bars, do you make them? Are they available from you? I am currently restoring a HBT7. 330-927-1876 OHIO
The HBT7 5174 was produced in Nov. 1959. This came from the British Motors Heritage Museum researcher. My title says 1961 Mark I, 4 seater, and the researcher agreed on the Mark I, 4 seater, but the 1959 production date and shippage to Minn, Minn Nov. 24 1959 really confuses me. Do I have a 1959 early production HBT7 that is miss titled ? If you any help would be appreciate. I’m on the auto list.
Thanks
Howard akronzips@aol.com 20 miles south of Akron,Ohio (no I missed the Conclave this year.)
1965 BSA A65 650
1969 BSA A50 500
1970 Triumph T120R Bonnie
1961 HBT7 5174 Tri- carb 4 seater
Great site:
Very,very helpful ideas especially the roll (sway) bars.I am currentlyrestoring a HBT7 5174 produced in Nov. 1959. The came from the British Motors Heritage Museum researcher. My title says 1961 Mark I 4 seater and the researcher agreed on the Mark I 4seater but the 1959 production date and shippage to Minn, Minn Nov. 24 1959 really confuses me any help would be appreciate. I’m on the ato list.
Thanks
Howard
1965 BSA A65 650
1969 BSA A50 500
1970 Triumph T120R Bonnie
1961 HBT7 5174 Tri- carb 4 seater